Phoenix 3D Printing transforms CAD designs into physical parts within hours, accelerating product development and shortening the time to market. For small-volume production, companies can replace expensive injection molding and machining with this technology.
Engineers use software to “slice” models into layers for Printing. This tells the printer where to add material for each layer of the final product.
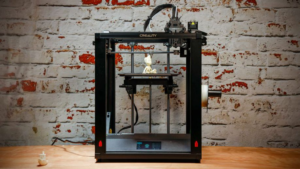
3D Printing is the process of creating objects by building them layer-by-layer using computer-aided designs. It’s an additive manufacturing process that contrasts with subtractive processes like CNC machining, in which portions of blocks of raw materials are carved out to form parts, and formative processes, which mold raw material into prefabricated moulds.
This transformative technology promises to democratize manufacturing, advance sustainability, and unleash greater creativity and innovation. 3D printers are gaining traction across industries, from healthcare and automotive to consumer electronics and fashion. As a result, there’s an ever-growing need for skilled professionals who can operate these advanced machines and create high-quality prototypes and finished products.
The most common applications for 3D Printing involve plastics, with a wide range of thermoplastics (acrylonitrile butadiene styrene, ABS, polylactic acid, or PLA) and resins. Other materials are emerging as viable choices for certain applications, including ceramics, metals, and composites, which can provide enhanced traits such as heat resistance or conductive properties.
Depending on the design, some prints may require post-processing to remove supports and finish the surface. These tasks can be time-consuming and require specific tools, including sanding equipment and specialized coating materials. In addition, workers should be trained on the safe operation of these sophisticated machines and their associated materials, especially if they’re working with hazardous chemicals or cutting tools.
With the right skills and a good understanding of how these machines work, professionals can maximize the benefits of 3D Printing to accelerate product development, streamline production, and reduce operational costs. This guide provides an overview of the different types of 3D printers, how they operate, and what to consider when purchasing one.
The first step is to determine which type of printer is best for your needs. This guide outlines the most popular options and highlights their unique capabilities. It also offers a comprehensive list of resources and tools to help you get started. This includes a directory of 3D printer manufacturers, a glossary of terms and acronyms, and links to additional resources, such as webinars and white papers. For more information, contact a Protolabs Network sales engineer.
Fused Deposition Modeling (FDM)
Fused Deposition Modeling (FDM) is a 3D printing technology that uses material extrusion. It is one of the cheapest types of 3D printers and is often used for prototyping purposes. FDM machines use thermoplastic filaments to create the parts. These are fed into the machine and are melted and deposited layer by layer onto a build plate.
The parts are then allowed to cool and harden into a solid. FDM is the most common type of 3D Printing at the consumer level and is typically a person’s first introduction to the broader concept of 3D Printing. It is also the most widely used type of 3D Printing in schools and university makerspaces.
The workflow for FDM, SLA and SLS 3D Printing consists of the same three steps: designing, 3D Printing and post-processing. Post-processing tasks can range from removing supports to rinsing and post-curing the final parts. These tasks can be automated with software solutions such as Fuse Sift and media blasting, reducing labor costs and improving consistency.
In addition to the cost of a printer, there is an additional cost associated with post-processing and materials. The cost of raw filament can be expensive and requires a certain amount of training and experience to use effectively. Additionally, sanding and smoothing parts can be time consuming and costly.
With an average price for an entry-level FDM printer around $200, hobbyists and small businesses are likely to use this technology for non-functional prototypes or production jigs and fixtures. It is also a popular choice for consumer goods manufacturing, as companies can quickly produce high-quality prototypes at a low cost to test product design and embodiment designs.
The desktop metal 3D printing process patented by Desktop Metal and Markforged Inc is similar to the FDM extrusion-based AM technology but instead of using thermoplastic filaments, bound metal rods are used as the feedstock for the process. These rods are made from a combination of metal powders and wax or polymer binders. This combination of materials allows the part to be a mixture of rigidity and flexibility. This is an important factor in ensuring that the printed part can meet functional requirements.
Direct Metal Laser Sintering (DMLS)
Direct Metal Laser Sintering is one of the more advanced additive manufacturing processes for producing metal parts. The process is a form of powder bed fusion, but differs from other powder-based printing techniques like Selective Laser Melting (SLM) and Binder Jetting in that it uses laser power to actually melt individual metal particles, instead of simply heating them. This results in greater part density, a more efficient production process and the ability to produce parts that are nearly as strong as conventionally formed materials.
The process starts with a digital blueprint, or 3D model, of the desired part which is then deconstructed into paper-thin layers that are uploaded to a DMLS machine. A thin layer of metallic powder is then dispersed across the build platform and the high-powered laser begins the process of sintering, or melting together, each particle based on the specifications dictated by the CAD file. The process continues in this manner, layer by layer, until the final part is complete.
Once the part is printed, it’s post-processed to remove any slag or residual material. It’s also heat treated and a surface finish is applied, just as it would be with a traditionally-formed component.
DMLS is a perfect solution for creating complex, highly-stressed metal components that might not be feasible with other AM technologies. It’s also an excellent option for creating lightweight metal parts, as it can significantly reduce the weight of a design without compromising strength. This advantage can save money on shipping and fuel costs in industries such as aviation and automobiles.
Because DMLS is such a sophisticated process, it requires extensive expertise to consistently produce high-quality parts. Fathom is one of the largest and most experienced sources for DMLS services in North America, working with a wide range of clients to deliver complex metal components, including aerospace, automotive and medical products. Whether your project involves titanium surgical instruments, aluminum body panels or gas turbine fuel injectors, our team of experts is well-equipped to help you get started with DMLS today. To begin your journey, upload your CAD files for an instant quote.
Selective Laser Sintering (SLS)
SLS is an additive manufacturing process in which thermal energy selectively fuses regions of powdered materials to create functional parts. It is also considered a part of the “powder bed fusion” category of 3D printing technologies (along with FDM and SLA).
The SLS printer builds parts by depositing fine, loosely packed powdered material onto a platform in the build chamber of the machine. The powder is then preheated to a temperature below the melting point of the raw material used. A spreading roller or arm then evenly distributes a fresh layer of the preheated powder over the platform in the print chamber.
Once the platform is covered in a thin layer of powder, the laser scans across the top of the model and heats specific regions of the powder above the melting point to solidify them into one integrated piece. The unheated portion of the powder acts as a support layer and allows for complex geometries, undercuts, thin walls, and negative features to be printed without the need for dedicated support structures.
Because the bonding between layers is so strong, SLS prints are durable and resistant to abrasions, making them suitable for many applications. They also have excellent mechanical properties, with strength resembling injection molded parts. In addition, the process is highly scalable and easy to use. It also produces parts with isotropic mechanical properties, meaning that the part’s strength is the same in all directions — unlike other additive manufacturing processes, which may have different strengths depending on how the part was made.
SLS machines typically have larger build envelopes compared to SLA and FDM printers, which means that they can produce more significant components in a single print run. They also offer faster production times than SLA and FDM thanks to the low power required for the laser beam to bind powders together.
While SLS has been a popular choice for professionals and enterprises for decades, its high price tag and demanding setup requirements have kept it out of the reach of most consumers. Industrial SLS printers require special HVAC and industrial power, have a steep learning curve, and can cost up to $200,000 for the most basic system. Because of these barriers, SLS has been largely limited to service bureaus and large enterprises with the capital to invest in such a solution.